7 Smart Solutions for Long-Lasting Floors
Kelowna’s beauty brings more than just sunshine—it brings humidity. And if you’re coating concrete, that moisture can silently wreck everything underneath your floor. At Prime Concrete Coatings, we see it time and time again: improperly sealed floors blistering, peeling, or failing entirely—not because of bad materials, but because of one overlooked factor: humidity.
Whether you’re working with a garage, a basement, a commercial kitchen, or an industrial space, understanding how to manage moisture is key to long-lasting results.
Why Humidity Can Break a Floor
Concrete is naturally porous. Water vapour from beneath the slab or in the air can travel up through the concrete. If it’s not properly addressed before coatings are applied, that vapour gets trapped—and when it has nowhere to go, it causes:
- Bubbling and blistering
- Peeling or delamination
- Efflorescence (that white, chalky residue)
- Complete coating failure
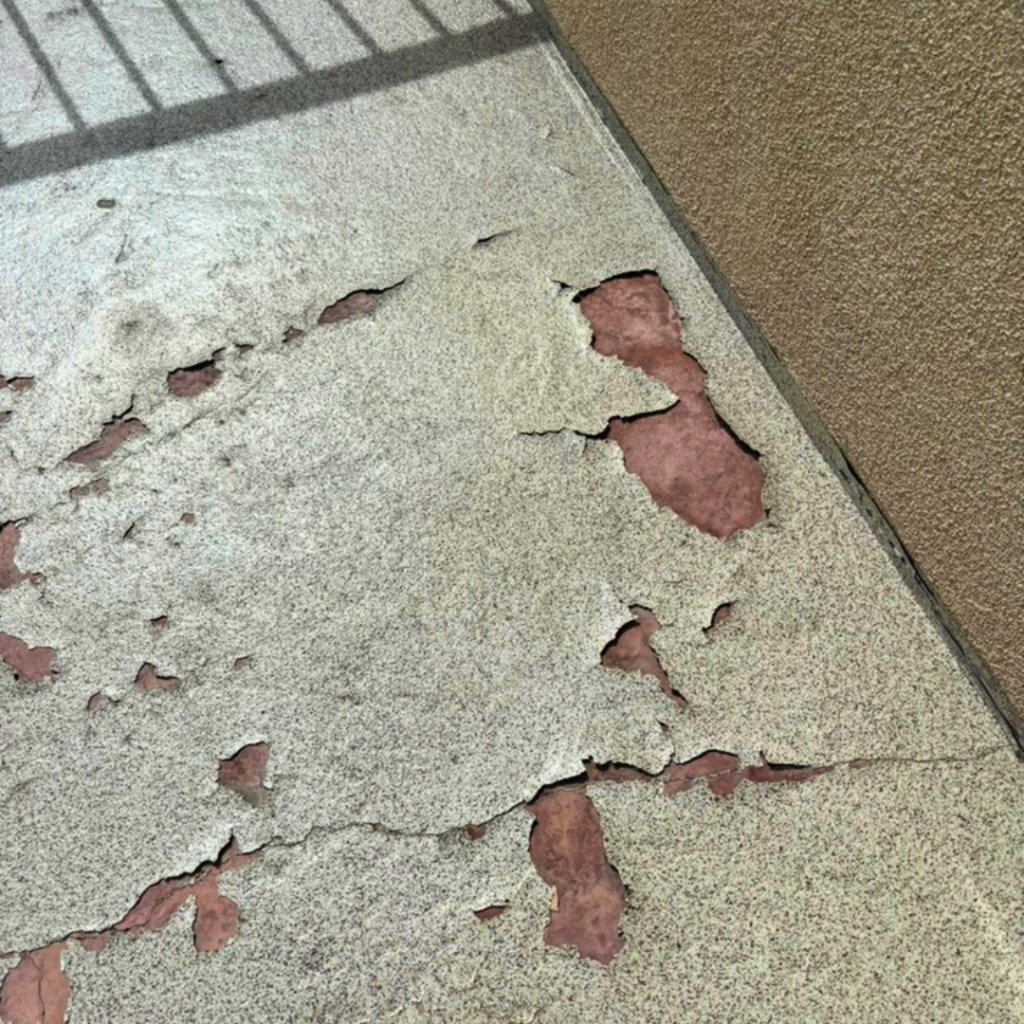
Even if the surface looks dry, moisture can still be lurking deeper in the slab. That’s why moisture testing is non-negotiable.
Our Process to Mitigate Moisture Right Way
At Prime, we don’t skip corners—or steps. Our moisture control process includes:
- RH (Relative Humidity) testing with probes for accuracy
- Application of moisture vapour barriers when needed
- Concrete profiling to open up the pores for proper adhesion
- Use of dehumidifiers, fans, etc for climate control during installation
- Carefully selected products suited for high-moisture environments
If our testing reveals elevated moisture levels, we apply moisture mitigation primers or barriers specifically formulated to seal the surface and allow proper bonding of the finish coat. This ensures a system that performs over time—not just one that looks good on day one.
The Right Products for the Right Conditions
Here’s where experience counts. Not all coatings are created equal, and not all work well in moist conditions. In the Okanagan, we’ve seen the best long-term results with hybrid systems that combine:
- Epoxy primers for strong adhesion
- Moisture-tolerant vapor barriers
- Polyaspartic topcoats for UV resistance and fast curing
This approach delivers durability, aesthetics, and moisture resistance in one system—perfect for Kelowna’s unique climate conditions.
Where Moisture Matters Most
If you’re wondering whether this applies to your space—spoiler alert: it probably does. High-humidity concerns often show up in:
- Garages with concrete that “sweats” in seasonal weather
- Basements with poor airflow
- Commercial kitchens and restrooms
- Locker rooms and gym spaces
- Warehouses with slab-on-grade concrete
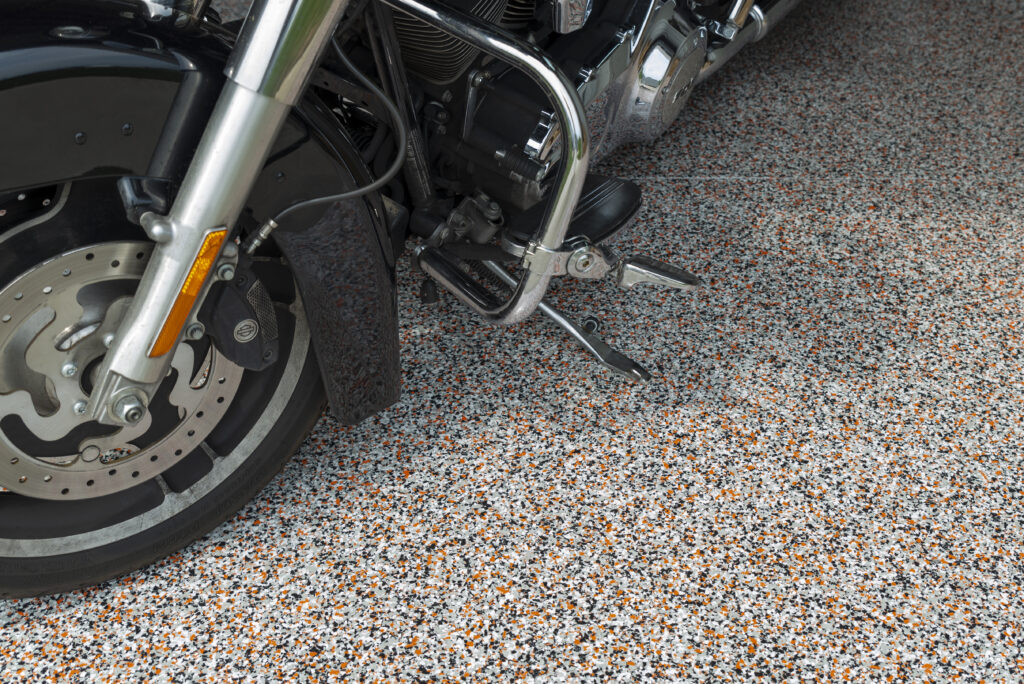
We’ve installed coatings in all of these environments, and we know what works. Our floor systems are chosen and customized with local conditions in mind.
What Happens If You Skip This Step?
Moisture mitigation may not be the flashiest part of the job, but it’s easily one of the most important. Without it, the finish may fail within months. That means:
- Re-coating at your expense
- Loss of use of your space
- Possible safety hazards like lifting or slipping
The cost of doing it right the first time is far less than fixing a failed floor. And we’re here to make sure that never happens.
Why Prime Concrete Coatings is Trusted in the Okanagan
We’re not just installing floors—we’re protecting investments. We test. We prep. We educate. And we build relationships with clients who care about quality.
Because at the end of the day, moisture is manageable—but only if you know it’s there and how to stop it in its tracks.
Ready to Build Floors That Last? Let’s talk about your space, your goals, and how we can create a concrete coating system that stands the test of time—humidity and all.